Heavy manufacturing industry in Georgia is one of the most important sectors in terms of value added, exports and employment. It is also one of the few areas where there are large companies with immediate opportunity for dramatic expansion. Growth in this sector, therefore, offers huge potential for providing broad economic growth, reducing unemployment, increasing tax receipts and improving Georgia’s balance of payments situation.
By comparison, in spite of its significance in terms of GDP, employment and exports, there has been little consideration of the heavy industry sector in the public discourse about economic development. As a result, the government has not supported growth in the sector and elements of the infrastructure that support the sector have continued to degrade. Equally importantly, the government has not promoted the sector in their investment promotion efforts and, as a result, opportunities for investment and growth have undoubtedly been missed.
If one looks at the sub-sectors, the numbers are similarly impressive. ‘Metal and metal products’ is worth 2.5% of GDP. ‘Chemical and non-metal mineral products’ (mostly fertilisers and cement) is worth 2.3% of GDP. This makes both of these subsectors roughly the same size as the entire telecommunications sector (worth 3% of GDP) or banking (worth 2.8%) and makes both sub-sectors far more valuable than the entire restaurant and catering sector (worth 1.9%) or the hotel sector (worth 0.6%). Another manufacturing sector, that of ‘transport and manufacturing equipment’ (worth 0.9% of GDP) is somewhat smaller but roughly the same size as manufacturing of alcoholic beverages- including wine (also 0.9%).
Of all of the sub-sectors a few are particularly important; manganese, steel, fertiliser, cement, trains, airplane parts, electrical wire and other metal products stand out. These sectors generally gain their comparative advantage from a combination of existing plant infrastructure and/ or available local inputs. The plants are often old but would be enormously expensive to replace and are often extremely well connected in terms of transportation infrastructure, physical buildings and electricity transmission provision. They also depend on the utilization of locally available resources, whether that is manganese, scrap metal, lime, aggregates, or relatively inexpensive electricity.
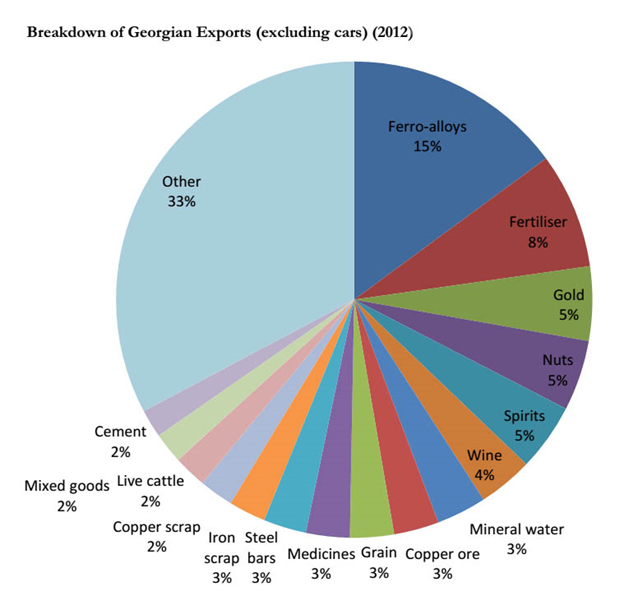
As one can see, the combination of ferroalloys, fertilisers, steel and cement is already 28% of total exports (excluding cars), and that does not include aircraft parts, railway carriages, steel pipe, plastic products and many manufacturing subcategories that are not big enough individually to be included in the separate categories.
It is hard to gain a clear national picture of the importance of heavy manufacturing because, generally, GeoStat does not publish data that is disaggregated in sufficient detail to see the value added of each sub¬sectors. Below is a breakdown of the main sub-categories, as presented by GeoStat and as subsequently explained in discussions with GeoWel in early 2013.
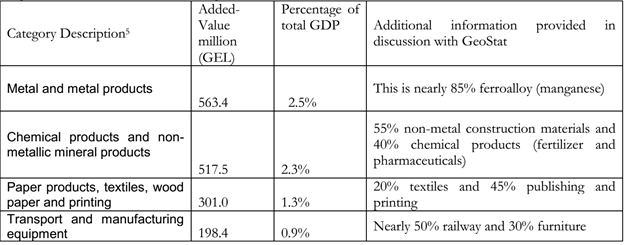
Metal and metal products (which is 2.5% of value added) and the construction materials/ chemicals sector (worth 2.3%) are similar in size to the entire telecoms sector (3%) or the banking sector (which is 2.8%).
In the discussion that follows, we will consider each of the key manufacturing sectors individually, to provide a quick overview of each. This list is not intended to be exhaustive, but should be indicative of the heavy manufacturing sector as a whole.
Ferroalloys Industry
Ferroalloy manganese is, as its name suggests, an alloy of manganese and iron. As we already highlighted, ferroalloy manganese is Georgia’s largest exports. Mining and processing of ferroalloy, according to discussions with GeoStat, also makes up around 85% of the GEL 500 million in value added in basic metal production.
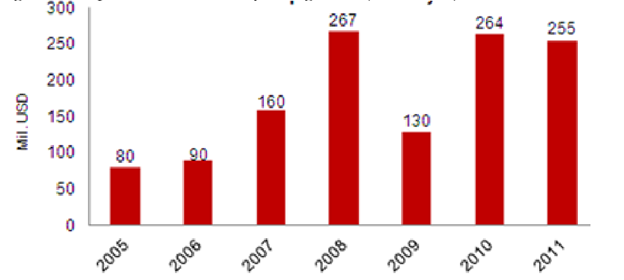
Manganese mining and processing largely takes place utilising industrial infrastructure built during the soviet period, though there are some smaller manganese processors in Georgia that have been built more recently.
Manganese is mined in Chiatura plant, by Georgian Manganese, LLC whose holdings includes the Chiatura manganese mine, Zestafoni ferro-alloy plant, and Vartzikha hydropower. Installed production capacity of Zestafoni ferroalloy plant is 185,000 tons per year.
The company extracts ferroalloy manganese as well as manganese ore-concentrates and manganese oxide, they then process some of the manganese in the Zestafoni plant. Chiatura manganese mine includes 4 mines and 3 open quarries. According to “Felman Trading Inc.”, who sell manganese from the mine in the US market, the total output of Manganese ore is 1.18 million tonnes and manganese concentrate is 0.4 million tons per year. Preliminary desk research uncovered a reference to Chiantura mine from 197 4 when it was believed there was a supply of 239 mln tones, or 160 years worth at current production levels.
Fertilizer Industry
As we have already seen, fertilizer is Georgia’s second largest export and, like manganese, relies on the utilization of former soviet industrial capital infrastructure that, while probably inefficient by modern standards, would be enormously expensive to build from scratch.
The supplier of the product is Azot LLC which is the only major producer of fertilizers in the South Caucasus. The company is situated in Rustavi and it is fully owned subsidiary of Agrochim S.A. The company hires more than 2000 workers.
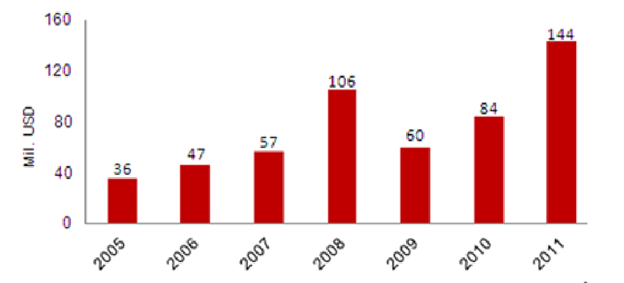
As one can see, production and exports dropped in 2009, as the result of the financial crisis, but have since then have surpassed their previous 2008 high, and are on track to grow further this year.
The technology used for the production of the fertilizer is heavy capital equipment built during the soviet period. This equipment fixes natural gas to produce a range of products, including Ammonia ( 400 000 Tn. Year), Nitric Acid (372 000 Tn. Year), Ammonium Nitrate (450 000 Tn. Year), Ammonium Sulfate (410 000 Tn. Year), Sodium cyanide (8 000 Tn. Year), Hanun (75 000 Tn. Year), Oxygen (78 300 Thousand m3), Dry ice (3 000 Tn. Year), Carbon dioxide (12 000 Tn. Year).
Steel processing sector
Steel processing is worth about 2.5% of GDP, when classified along with ferroalloy. Taken in itself, it is worth about 0.4% of GDP. As has already been mentioned, this makes it about 2/3 the size of the entire hotel sector. The sector is dominated by Rustavi based steel producers, which mainly consists of the large Rustavi Metallurgical Plant and GeoSteel, and a smelter in Kutaisi, owned by Eurasian Steel Ltd. In addition, there are several dozen small smelters across the country, mostly in the old industrial cities.
It is hard to be sure how many people are employed in the sector at the current time, but local experts estimate somewhere around 3000.
The steel sector in Georgia mostly consists in the melting and processing of scrap metal, though some parts of the industry also import particular grades of steel for the production of metal products. This makes the sector heavily exposed to scrap metal exports, as the more scrap is exported, the less is available for local processing.
Historically in Georgia scrap metal has been the bigger business. Until 2005 scrap iron was one of the country’s principle exports, with much of the iron, ironically, coming from the scrapping of the Rustavi Metallurgical Plant processing infrastructure.
However, as Georgia’s economy has diversified, and as the steel processing sector has grown, scrap exports have fallen. Scrap iron is now worth 3% of exports, and is slightly lower than processed steel bar
Cement Industry
Another large contributor to GDP, with about GEL 250 million of added value, is non-metal construction materials. This is made up of a range of different materials that are extracted and processed, including lime, chalky soils, gravel and decorative stone.
Cement is particularly prominent. The two biggest cement plants are Kaspi Cement and Rustavi Cement, which are both 75% owned by Heidelberg Cement. The Kaspi plant is the first cement plant in Georgia, constructed between 1927 and 1931 years. The plant was restored between 2000 and 2006, and later on, merged with Rustavi plant under the common corporate name “SagCementi Ltd”. After large capital investment, the production of two plants became 1.6 million tons per year.
Heidelberg Cement also acquired 70% of Kartuli Cementi Ltd in May 2006 and relocated a modernized plant from Kiefersfelden, Germany to its Rustavi site. This new plant started working in January 2008, and has a capacity of 400,000 tons of cement per year.
Interestingly, while added value for ‘non-metal construction materials’ remains high in Georgian national statistics, and Heidelberg cement has reported strong growth, exports of cement have declined precipitously since 2008.
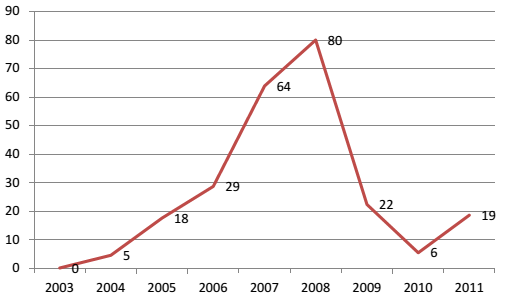